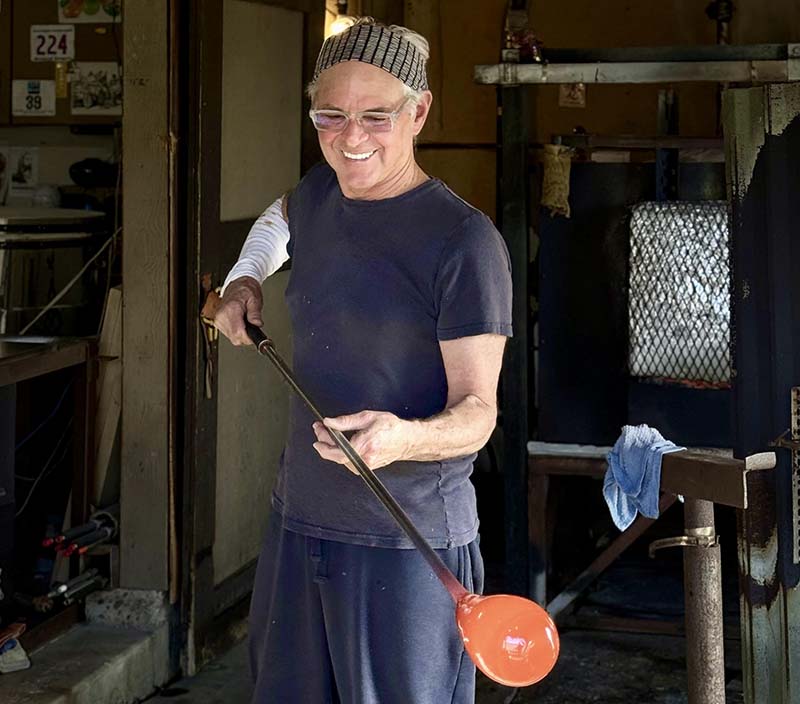
Vizzusi’s Glass Featured in Collections Around the World
For the past 40 years glass artist Peter Vizzusi has been blowing molten glass into wildly colorful tumblers, goblets, bowls, and just plain beautiful objects. Based in Santa Cruz, Vizzusi’s studies in the Bay Area and Italy fueled his ambitious career. Now his blown artglass can be found in museums and collections all over the world. – Christina Waters
Q: How did you chose making glass art as a profession?
PV: I found my life’s work, inadvertently- seeing hot glass action across the hall from the ceramics studios at San Jose State where I was an avid student, then at Old Town, Los Gatos, where the self-styled glass maesetro Rick Strini had built a rudimentary furnace. Then, fortuitously, during the Italian section of my post-college European tour, hopelessly lost, in November, cold and wet, in the Venetian maze, I boarded the wrong vaporetto and ended up out on Murano where I strolled past a dozen glass studios; furnaces blazing, alive with hot glass activity. One particular shop seemed welcoming, and I warmed myself, shared some of my American cigarettes, and watched them make some generic tourist ware.
Q: How did it all start for you? a class? a whim?
PV: By age 24, I caught the wave of 1970s, post-college, baby-boom entrepreneurial energy, and landed a hot glass job in Santa Cruz making stems, feet, and ceramic accessories and working the booth at the Renaissance Fairs in Novato and L.A., bringing our early goblets and art vessels directly to the market. This early to mid-70s era was the perfect environment for self invention. Glass artists salvaged, scavenged, re-purposed, repaired, and appropriated when necessary. We spent more time in scrap metal yards than in museums. I traded my sports car for a pickup, grew a beard to look older, learned some very basic combustion engineering and safety systems, got a permit, and built my own studio at the Santa Cruz Art Center.
Q: What prepared you for a life in glass?
PV: I was a decent ceramicist, I could build things (my dad was a craftsman, a draftsman, and a general contractor), I surfed with my future boss, was ambidextrous with good depth perception. I was attracted to the intense heat, and was generally available.
Q: What do you love about it most?
PV:
Initially I was attracted to the rhythm, choreography, and immediacy of glass making, and I still enjoy the meditative repetition of a productive day. I’m proud to identify as artigiano, working with traditional techniques, guided by my own design sensibility. On rare occasions, I’ll wander into the studio and be inadvertently surprised by my own work—the shapes, colors, the iridescence, the textures, and patterns; as if someone else had made them, with myself as medium, briefly communicating with long-forgotten glass masters.
I immediately understood that “perfect” is the enemy of the good. It’s about using what works and making it the best it can be.
Q: What is your philosophy of making an authentic piece of studio glass?
PV: I consider myself third wave studio glass. I’ve been comfortable and productive, working, almost anonymously, making interesting and functional vessels that fit a variety of decorative interior applications. Clarity and simplicity of line are the most important elements. Even creating functional vessels myriad qualities of the molten glass inspires self expression.
Q: What is your advice to someone considering a career in the crafts?
PV:
Dive deeply into your chosen medium, specialize, master at least one technique, experiment, and find your own voice. Know your audience and make something they absolutely can’t resist.
Peter Vizzusi, Magic Sands Glass Studio 831.688.6167, by appointment
By Christina Waters


One Comment
Larry Wall
Very interesting article. I have purchased a few of Peter Vizzusi’s drinking glasses over the years, and I must say even a glass of water taste better with them. Peter is certainly a master of what he produces.